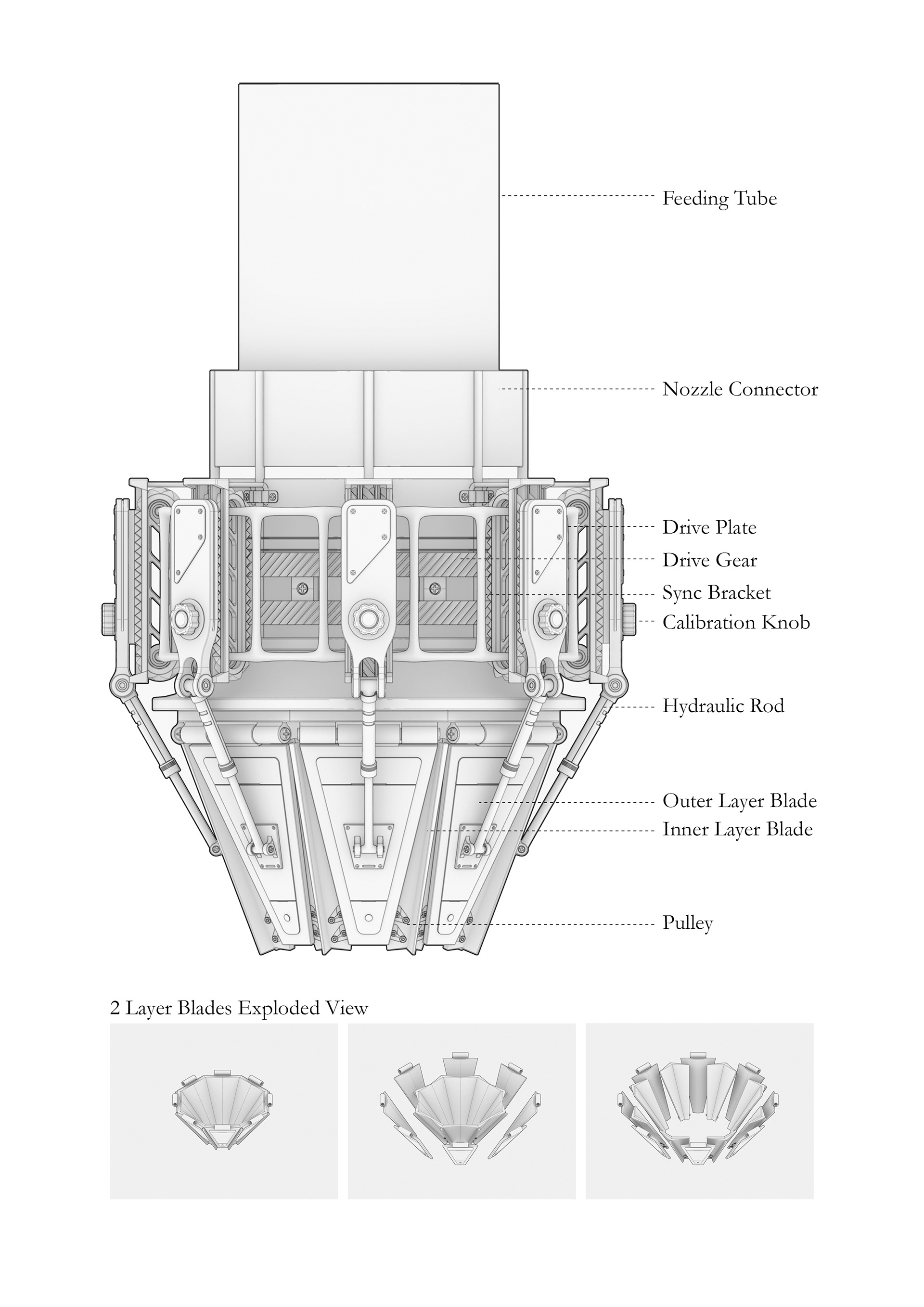
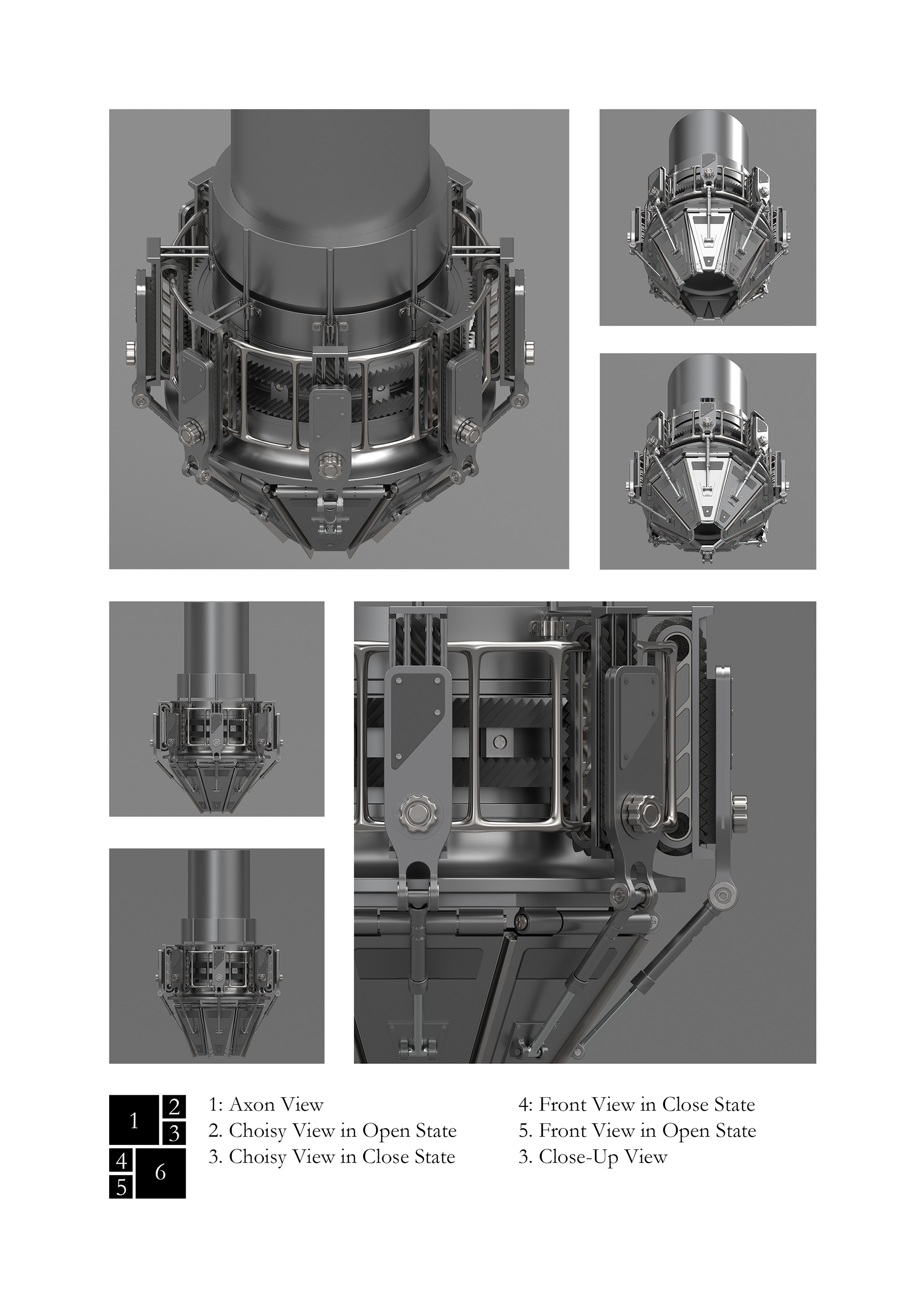
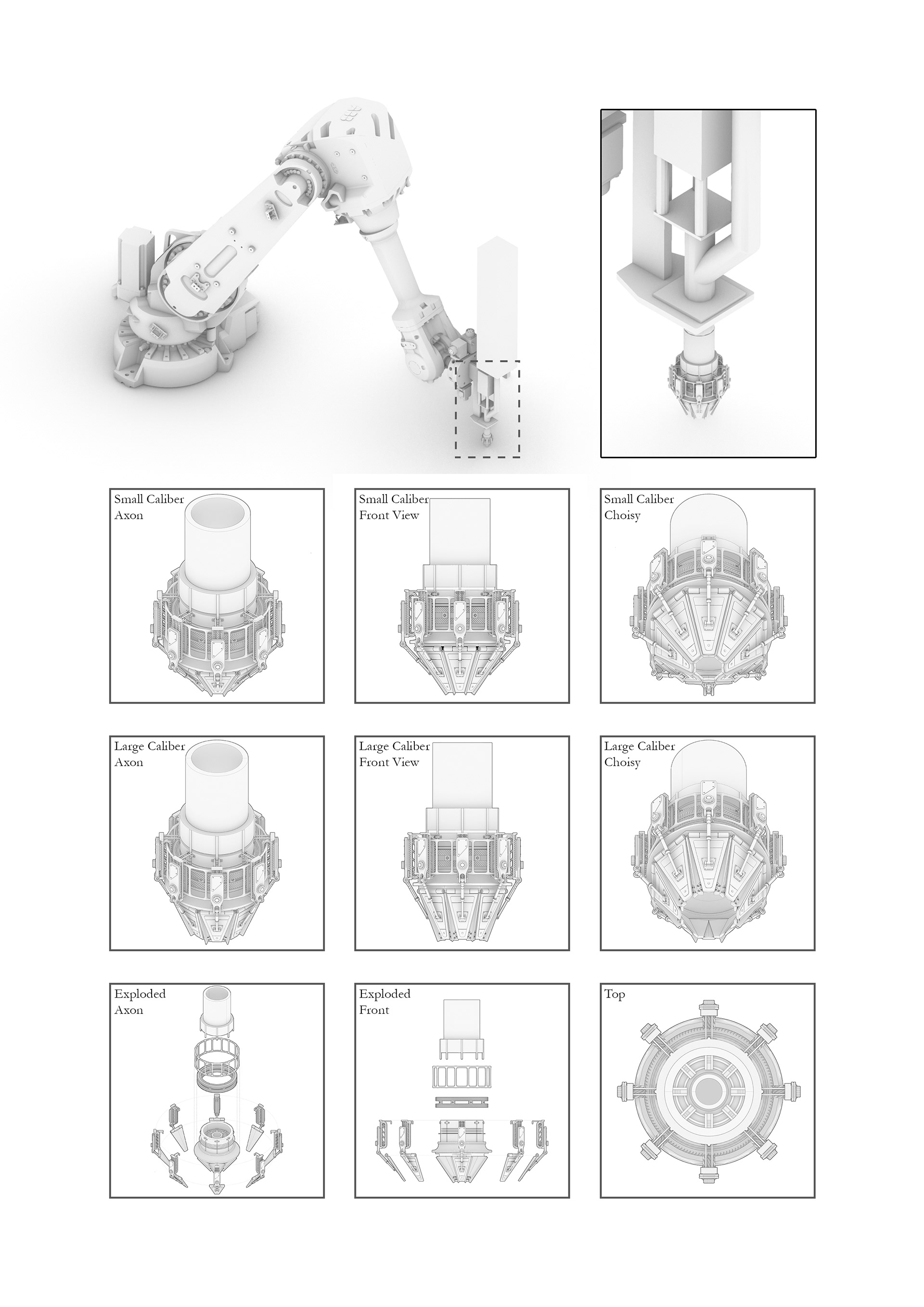
The idea of this conceptual object is an end effector. Its main function is to continuously change the nozzle diameter during the robot arm printing in order to have more flexible control over the printing process.
The need for different print thicknesses is encountered in the processes of printing ceramic artworks and concrete buildings by robotic arms. Traditional print nozzles are fixed diameters, when encountering different thickness requirements, the only way to print is to stop printing and temporarily replace the nozzle with another diameter, which causes inconvenience and creates unwanted breakpoints. Here we wish to propose a variable nozzle that can be used for robotic arm end effectors, by taking inspiration from the mechanical structure of jet afterburner nozzles.
This printing nozzle is capable of constantly changing the extrusion aperture during printing, depending on the preset thickness requirements. As above, the mechanics are similar to those of an afterburner nozzle: the nozzle has two layers of blades, both of which are closed at the smallest diameter and both of which are open at the largest diameter.
The working process is as follows:
1. the upper motor drives the gears, and the teeth of the gears in an oblique direction drive the outer plate upward.
2. when the drive plate is pushed upward, it acts together with the hydraulic rod below on the outer layer of the blades to pull it open.
3. the opening of the outer layer of the blades drives the inner layer of the blades to open, and the whole nozzle is in an enlarged state.
Notes:
1. The mechanical structure in the two layers of blades controls the opening and closing amplitude and prevents the gap in the middle of the blades from causing the extrudate to clog the gap between the inner and outer blades.
2. The drive plate is connected to the syn bracket to ensure the synchronous movement of the eight drive plates.
3. A leveling knob on the drive plate allows manual calibration of the precise position of the eight blades.